中國冶金報社
通訊員 殷藝
2024年,酒鋼東興鋁業公司迎來一項里程碑式突破——電解原鋁液通過中國有色金屬工業協會綠色產品評價中心認證,正式獲得綠電鋁產品評價證書。
這張“綠色身份證”的背后,是酒鋼集團十余年如一日深耕綠色發展的縮影,也是其以綠色發展重塑產業競爭力的生動實踐。如今,綠色競爭力,正成為酒鋼在行業周期波動中穩舵前行的底氣。
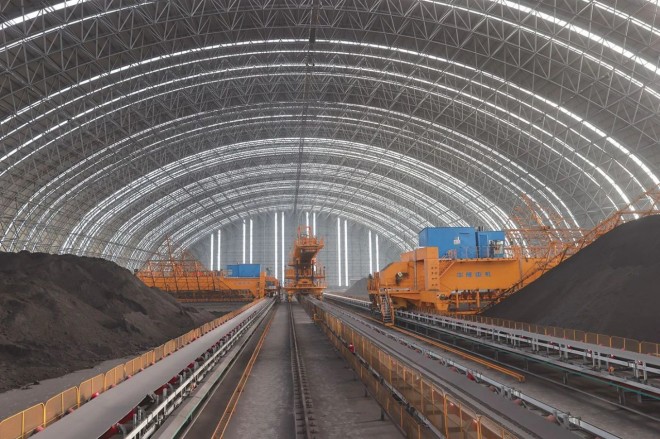
圖為酒鋼宏興股份公司儲運部嘉東料場綠色智能化改造項目混勻料場內部。 (張志方 攝)
升級綠色管理——
精準降耗,構建低碳發展新體系
走進酒鋼廠區,儲運部嘉東料場的“三化”改造令人耳目一新。這座投資19億元的綠色料場,通過“用煤不見煤、運料不見料”的清潔生產模式,每年減少揚塵排放超90%。這是酒鋼構建綠色管理體系的一個切面。
緊盯“雙碳”目標,酒鋼將綠色發展上升為企業戰略,編制《碳達峰碳中和實施方案》,明確6大工作路徑、36項重點任務,形成“清單化管理、臺賬式落實”的推進機制;成立能源、碳排放專職管理機構,鋼鐵、電解鋁、電力能源三大主業在行業內率先建立全流程碳排放管理體系,宏晟電熱公司等5家單位完成能源管理體系貫標認證,實現10家重點用能單位能源管理體系全覆蓋。
通過構建產品全生命周期碳足跡評價管理體系,酒鋼梳理形成66個產品碳足跡認證重點產品及工作推進計劃,2024年順利完成430鐵素體不銹鋼等3款產品的碳足跡認證;鋼鐵、電解鋁、電力能源3大主業完成關鍵因素識別等工作,促進酒鋼碳排放管理水平持續提升。
這一系列舉措,讓酒鋼的綠色管理從“被動合規”轉向“主動引領”。2024年,酒鋼38項重點能耗指標同比進步,其中供電煤耗,本部焦化、高爐工序能耗等指標達到歷史最好水平;能耗、碳排放總量分別同比降低15.5萬噸、67萬噸,噸鋼、噸鋁碳排放強度同比優化,碳市場履約能力顯著增強,為行業提供了可復制的管理范式。
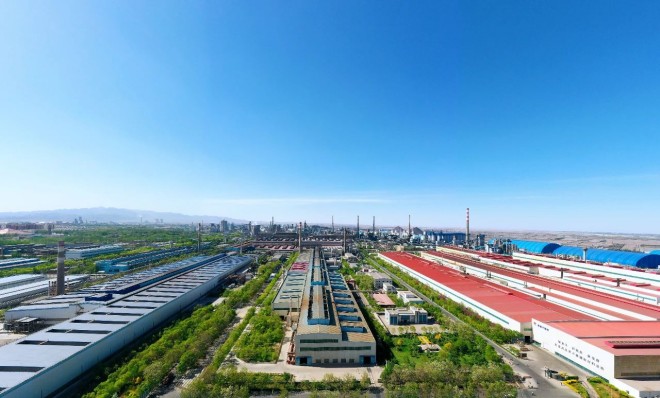
改進綠色工藝——
智能高效,以技術革新驅動“超低排放”
在酒鋼宏翔能源公司,1號、2號焦爐的化產區域曾是VOCs(揮發性有機物)治理的難點。如今,新采用的“洗滌預處理+RTO蓄熱爐熱氧化反應”工藝、新配置的化產逸散氣治理系統,將1號、2號焦爐逸散的廢氣收集凈化,煙氣排放指標穩定達到超低限值。這樣的蛻變,源于酒鋼對生產工藝的綠色再造。
酒鋼投資153.08億元實施35個鋼鐵超低排放改造項目,涵蓋燒結機升級等關鍵環節,如煉鐵廠1號高爐超低排放改造及大修項目對高爐原料供料系統、上料系統等進行優化改造和更新,實現各項環保指標達標。
新能源布局為減排注入新動能。酒鋼240萬千瓦智慧電網及新能源就地消納示范項目納入國家沙漠、戈壁、荒漠大型風電光伏基地項目建設清單,其中120萬千瓦風光電項目已并網發電。此外,投酒鋼資1.91億元建成的兩個光伏項目年發電量達1.07億千瓦時,年節約標準煤3.2萬噸、減碳8.9萬噸。
打造循環經濟——
深挖潛力,開辟市場增長新賽道
在酒鋼東興鋁業公司的生產線上,通過技術創新,炭渣被回槽消化為再生電解質,鋁灰經無害化處理后提煉出高純度鋁豆,廢舊導桿則成為下游產品的優質原料。2024年,東興鋁業公司通過技術創新與管理升級雙輪驅動,探索出一條“資源—產品—再生資源”的高效循環路徑,實現直接經濟效益2.8億元,鋁制品再生利用率提升至80%,實現了從“付費處置”到“競價盈利”的跨越。
這一轉型的背后,是酒鋼對循環經濟體系的深度構建。企業以“減量化、再利用、資源化”為原則,打通鋁產業鏈內部循環:電解鋁產線將廢鋁熔煉為高純度鋁液,回供下游加工;鋼鐵產業利用鋁灰作為鋼渣促進劑,年處置量達2萬噸;循環經濟產業將粉煤灰、脫硫石膏轉化為建材原料,形成跨產業協同的循環網絡。
如今,酒鋼已有2家單位獲評為國家級綠色工廠,2座礦山被納入全國綠色礦山名錄,成功發布連續熱浸鍍鋅系列合金鍍層鋼板及鋼帶和不銹鋼鐵素體、馬氏體、奧氏體、雙相冷軋板及鋼帶等5類產品的環境產品聲明。
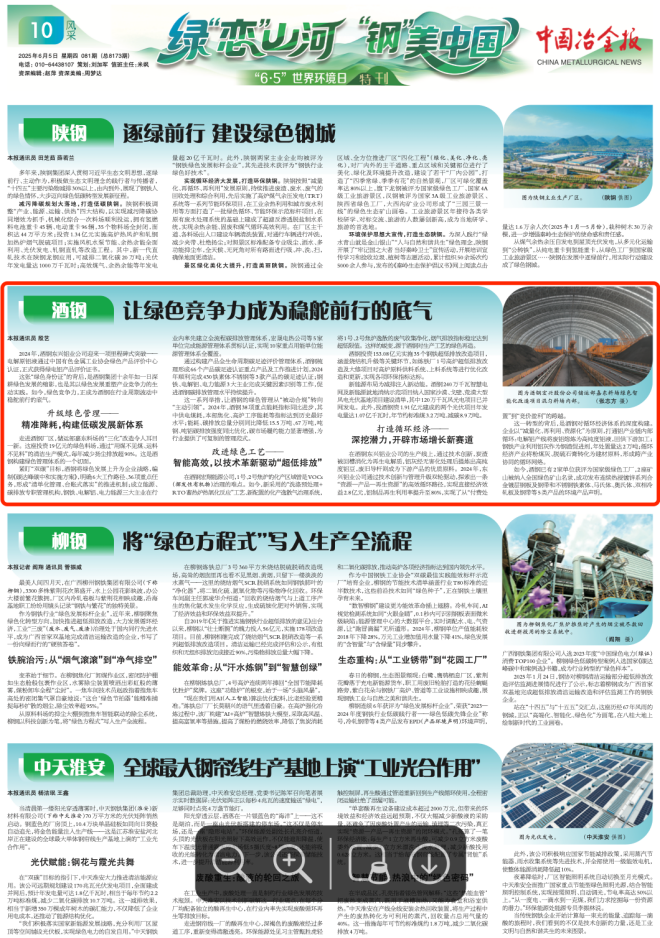