中國冶金報社
記者 夏杰生 報道
5月7日9時39分,隨著第一爐鐵水奔涌而出,由聯合榮大企業集團公司(下文簡稱聯合榮大)負責爐缸整體澆注和噴涂的寶武集團某公司4000m3級高爐在完成爐役大修后正式開爐復產。此舉為該公司實現全年生產經營目標創造了有利條件。
據聯合榮大董事長章榮會博士介紹:該項目既是對高爐本體的高標準修復,也包括根據國家環保等要求的一系列節能環保改造,使該高爐的后續生產運行將更為智能、綠色、經濟、高效,也將對寶武高質量發展產生積極而深遠的影響。
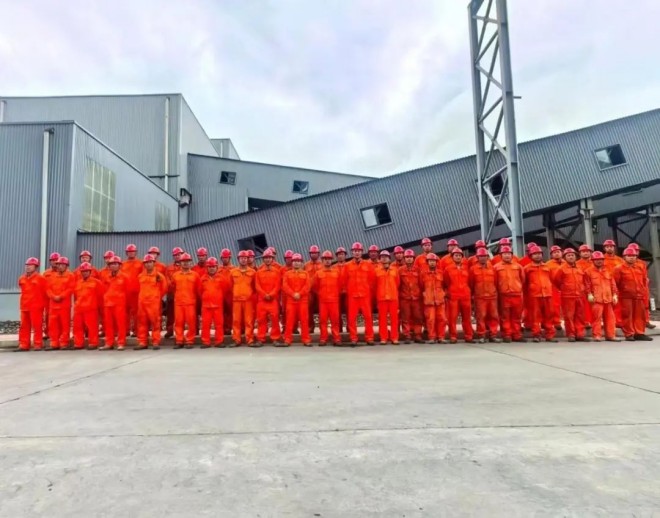
檢修方案 科學合理
章榮會博士指出:寶武集團在高爐大修中首次采用聯合榮大創新研發的爐缸整體澆注技術的最大容積高爐。該高爐因爐缸侵蝕嚴重,業主選擇在高爐大修工程中經驗豐富的聯合榮大對其進行大修。為保證檢修過程中的安全生產,消除隱患,聯合榮大憑借其多年高爐維修經驗,結合高爐具體情況,制定了如下檢修方案:
一是待爐缸清理完畢后,在砌筑環碳過程中,每砌筑三至四層時,采用高導熱澆注料進行一次碳磚與冷卻壁熱面之間澆注,代替炭素搗料,以實現整體質量和工期的兼顧。
二是對于爐缸和風口帶修復,待環碳全部砌筑完畢后,采用高爐爐缸澆注料對爐缸(包括鐵口通道和泥包)及風口帶進行整體澆注修復;
三是在內襯噴注過程中,采用高爐內襯剛玉碳化硅噴涂料,并采用人工抱槍噴注修復爐腹,恢復高爐操作爐型。
上述檢修方案不僅科學合理,更被聯合榮大人完美實施,確保了檢修工程一氣呵成,實現最終工期用時178小時(7.4天)比計劃工期提前16小時,創造了同立方米級別特大型高爐爐缸整體澆注施工時間最短的新紀錄。
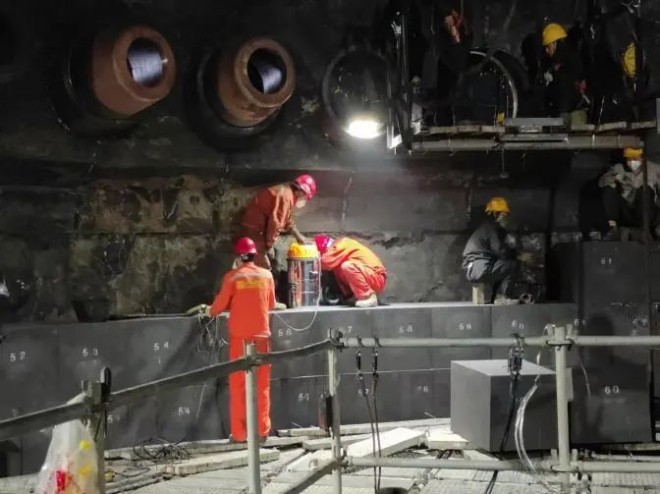
圖為縫隙清理吸塵
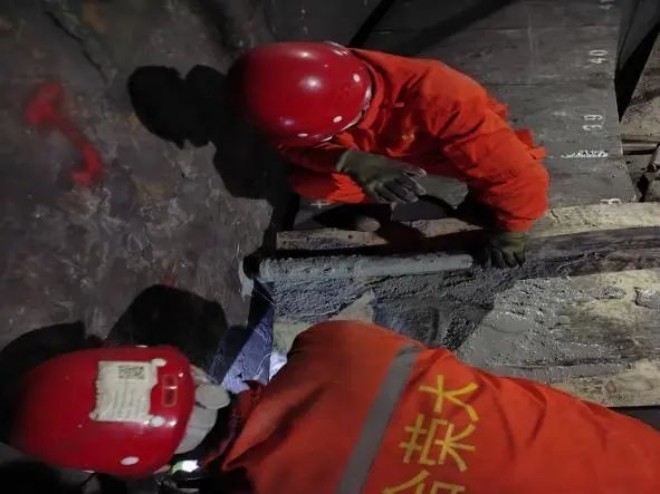
圖為縫隙澆注
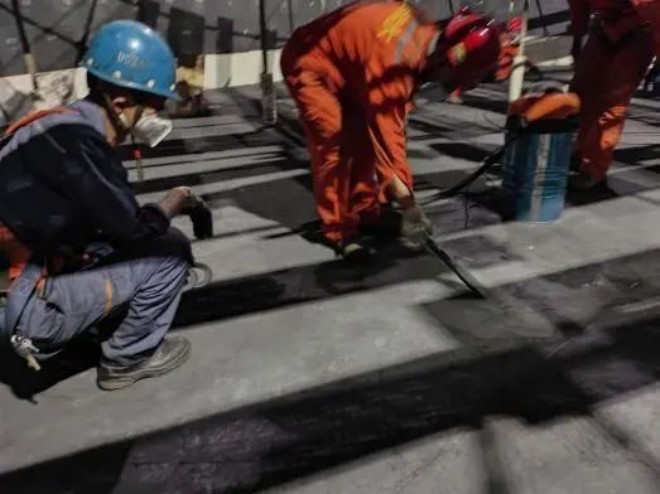
圖為爐底吸塵
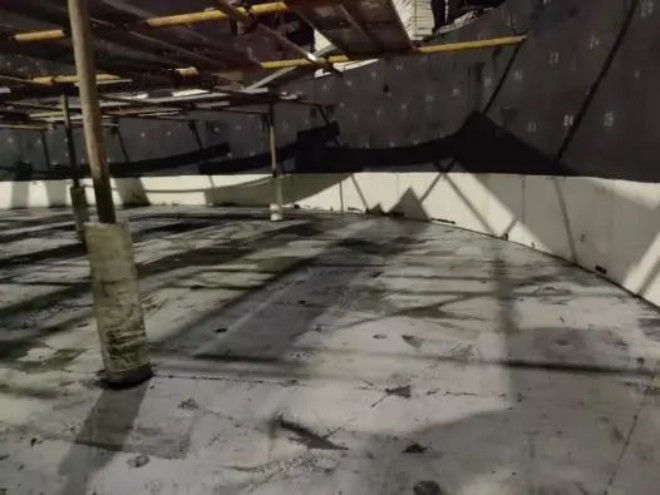
圖為涂刷界面劑、預留膨脹縫
精心施工 有條不紊
談到該高檢修具體過程,章榮會博士如數家珍。首先,在高導熱澆注料澆注,即環碳砌筑過程中循序漸進和爐缸砌筑施工方密切配合,在不占用主線工期的情況下順利完成。聯合榮大的施工人員在每砌筑三至四層后,采用高導熱澆注料對碳磚與冷卻壁熱面之間縫隙進行澆注密實。在砌碳磚期間分四次進行了澆注,不占主線工期。
其次,在爐缸施工工程中,結合現場實際情況想方設法提高支模效率,科學合理地僅用八模即完成所有澆注。
該特大型高爐檢修施工工程計劃工期194小時,實際用時178小時(7.4天),比計劃工期提前16小時。
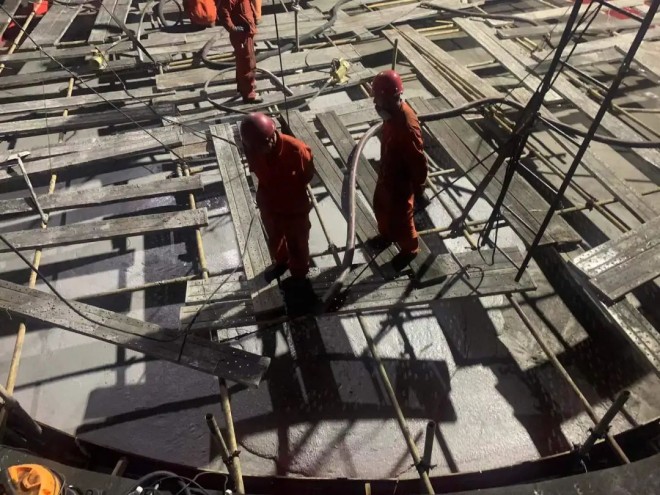
圖為澆注施工現場
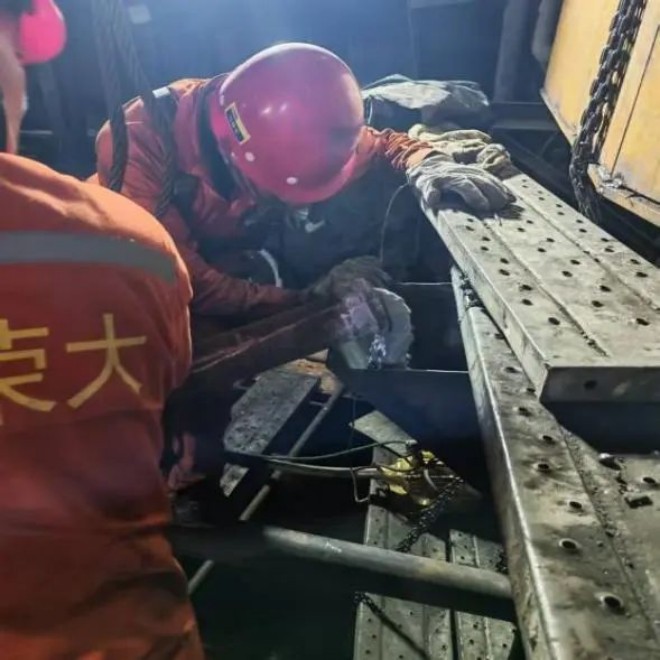
圖為鐵口澆注
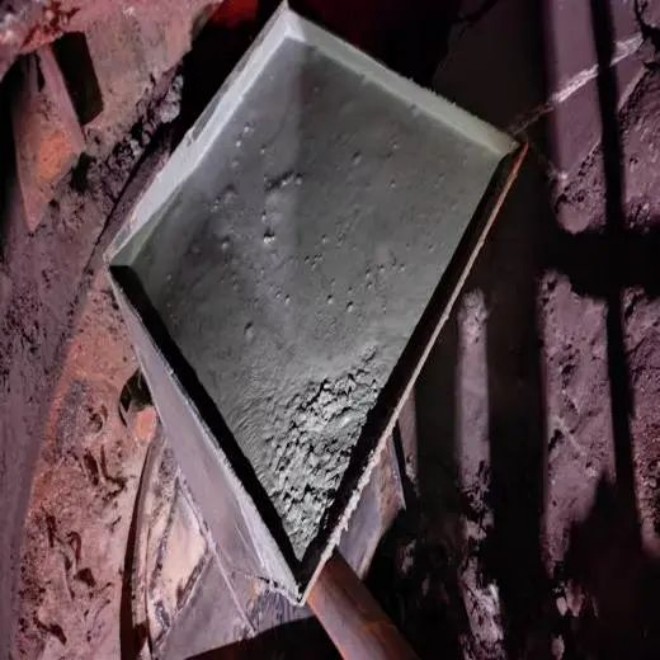
圖為鐵口澆注完成
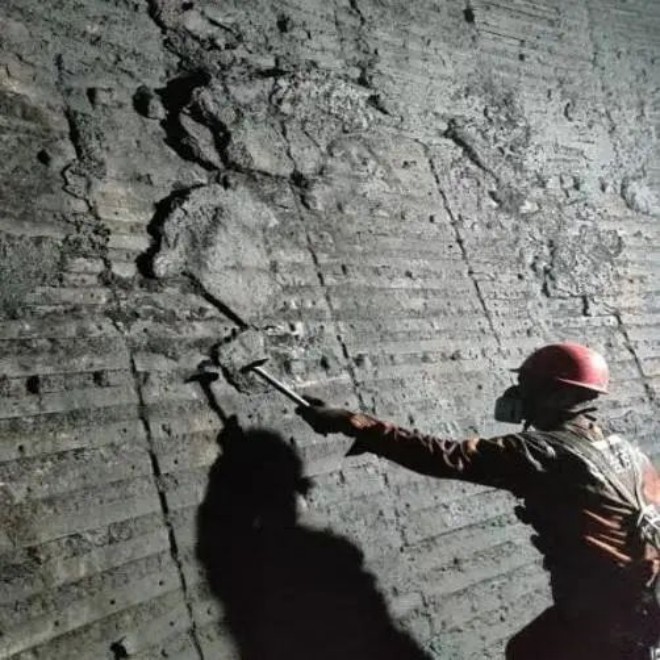
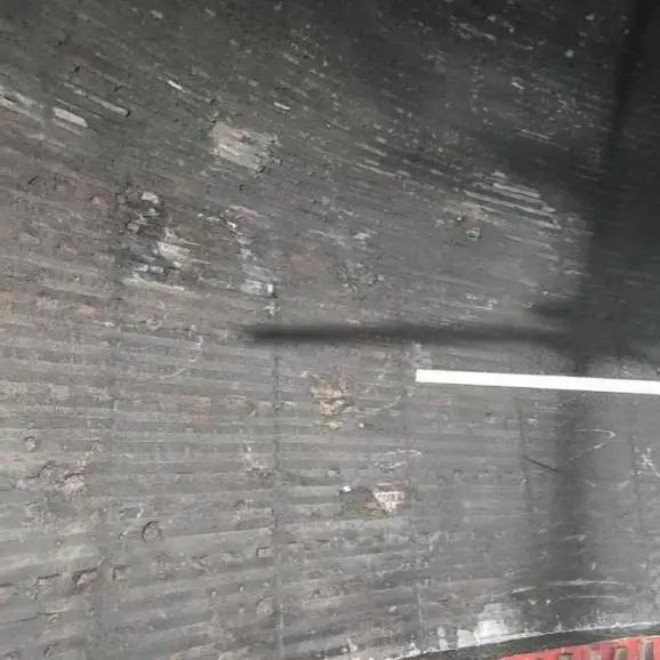
圖為噴涂前清理冷卻壁表面
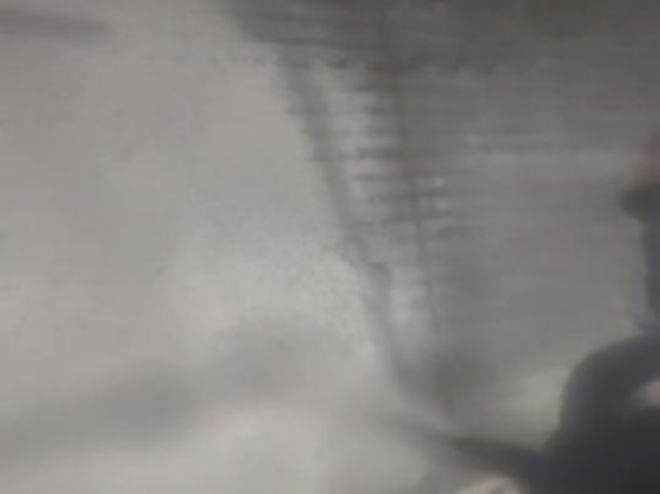
圖為噴涂
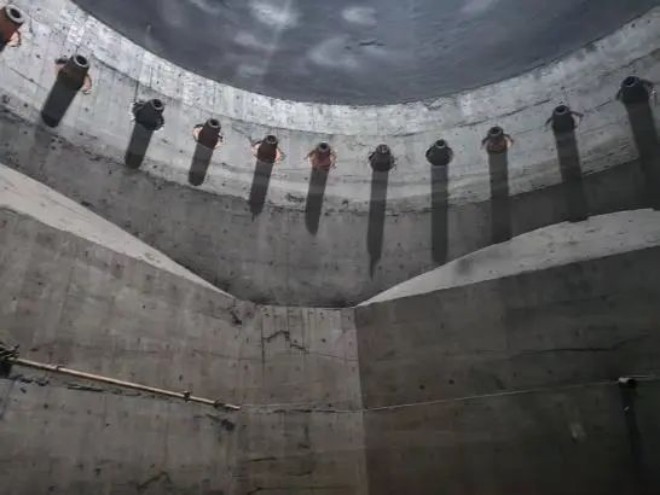
圖為澆注完成
亮點頻出 堪稱典范
章榮會博士認為:此特大型高爐檢修工程亮點頻出,堪稱典范。
一是工期得以充分保證。即此次噴涂作業未用吊盤,采用原腳手架起高,周圈搭設跳板,作業人員站跳板噴涂。相比于吊盤噴涂,節約了吊盤時間8小時。
施工前期施工隊長和技術人員反復磋商,制定合理工期計劃,根據材料特性及澆注厚度,制定每模最佳養護時間。將開始計劃的九模澆注改為八模澆注,減少一次爐缸澆注界面,更有利于爐缸澆注的整體性,難點是每模模板高度增加,最高一模模板兩米高,澆注料密度大,有跑模風險,增加了支模難度,根據現場情況,調用經驗豐富的支模人員,增加支模固定點,確保了支模萬無一失。減少一次支模養護時間,從而縮短了工期。
此次施工過程順暢,施工組織緊湊,各道工序無縫銜接,每一模均能提前完成,最終僅花178小時(7.4天)完成施工任務,比計劃工期提前16小時,創造同立方米級別高爐爐缸整體澆注施工時間最短新記錄。
二是物料組織合理流暢。由于材料合同簽訂較晚,4月15號才簽訂,要求18號前材料到場,聯合榮大在未簽訂合同情況下,提前生產,做好隨時發貨準備,合同簽訂后立即發貨,車輛進廠手續提前安排專人辦理,最終17號第一批材料到場,此后按照施工節奏,材料陸續全部到場,滿足施工進度要求。
三是施工組織嚴謹規范。為壓縮工期,改變以往最多兩臺設備同時澆注的模式,實行創紀錄的三臺澆注設備同時澆注模式,每小時澆注量接近40噸,同時現場做到澆注設備三用兩備,以防澆注過程行車故障,現場雇用一臺汽車吊隨時備用,極大保證了工期。
四是人員組織精明強悍。聯合榮大高度重視此次施工,項目經理、施工隊長、技術員、安全員均設兩套人員,分白夜班全程值守,施工人員均為聯合榮大正規在職職工。他們都有著多年的支模澆注施工經驗,做到施工進度、質量可控。
談到此次檢修工程的體會和感受,章榮會博士認為:此次爐缸整體澆注項目在安全前提下,保質量保工期,圓滿完成,得益于鐵廠各級領導及項目指揮部、高爐技術專家的全程悉心指導和大力支持,使整個施工過程極為順暢,注重施工細節,確保質量;也是對時間就是金錢,效率就是效益的再次詮釋。